Fraunhofer IPA: Methode zur Produktion von Festkörperbatterien
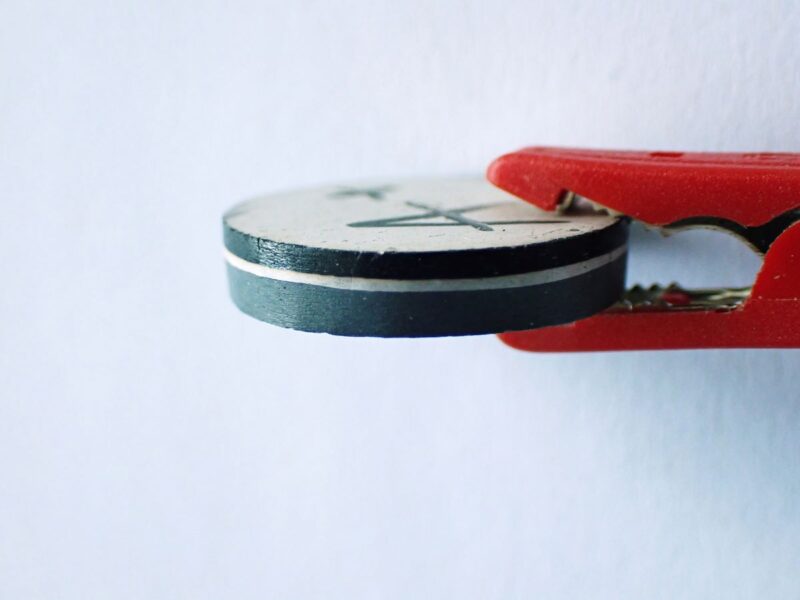
Das Fraunhofer IPA hat gemeinsam mit Partnern eine skalierbare Produktionsmethode für Festkörperbatterien entwickelt. Dies geschah laut Mitteilung m kürzlich abgeschlossenen Projekt EMSiG. Festkörperbatterien böten zahlreiche Vorteile gegenüber Lithium-Ionen-Akkus. Sie seien beispielsweise nicht brennbar.
Üblich seien bisher zwar Lithium-Ionen-Batterien. Doch Festkörperbatterien punkteten mit gewichtigen Vorteilen. Vor allem böten sie eine höhere Sicherheit. Schließlich haben sie keinen flüssigen Elektrolyten, der auslaufen und sich entzünden kann. Auch ist ihre Energiedichte höher, die Lebensdauer länger. Das Manko: Bisher wurden Festkörperbatterien mit einer Elektrolyt-Schicht aus Keramik nur im Labormaßstab gefertigt.
Forschende des Fraunhofer-Instituts für Produktionstechnik und Automatisierung IPA haben im Projekt »Erforschung neuer Misch- und Sintertechnologien für gradierte keramische Festkörperelektrolyte«, kurz EMSiG, nun die Grundlagen gelegt, um die Festkörper-Lithium-Ionenbatterien industrienah weiterzuentwickeln. Partner war das mittelständische Unternehmen Dr. Fritsch Sondermaschinen GmbH und Dr. Fritsch GmbH & Co. KG. Das Land Baden-Württemberg gab ferner eine Förderung von einer Million Euro. »Wir konnten die Produktion der Festkörperbatterien vom Labormaßstab auf ein industrienahes, skalierbares Level heben«, sagt Jonas Heldt, Wissenschaftler am Fraunhofer IPA.
Rohstoffe bisher Mangelware
Sollen Festkörperbatterien den Sprung in die industrielle Anwendung schaffen, braucht es zunächst einmal ausreichend Rohstoffe. Doch für die benötigten Ausgangsmaterialien – etwa der im Projekt eingesetzte Festkörperelektrolyt Lithium-Aluminium-Titan-Phosphat (LATP) – gibt es bislang keine industrielle Verwendung. Daher existiere auch keine größere Produktion. Der Projektpartner Dr. Fritsch GmbH & Co. KG analysierte deshalb die Marktlage. »Die Herausforderung ist hier nicht die Verfügbarkeit der einzelnen Rohstoffe an sich, sondern die noch relativ geringe Anzahl von Herstellern, die daraus das Festkörperelektrolyt LATP fertigen“, sagt Elke Ade, Leiterin Geschäftsbereich Metallpulver bei der Dr. Fritsch. Erfahrungsgemäß werde diese aber mit der Nachfrage nach dem Endprodukt schnell wachsen.
Neben einer gesicherten Rohstofflage sind industrienahe Produktionsprozesse gefragt, die sich auf einen größeren Durchsatz hochskalieren lassen. Klassischerweise beschichtet man Folien, damit sie als Anode, Kathode und neutrale Zwischenschicht dienen, und setzt diese zur Batterie zusammen. Bei Keramiken diene dagegen Pulver als Ausgangsmaterial. Um dieses in eine feste Form zu bringen, muss es gesintert werden – also unter Druck erhitzt. Dazu untersuchte das Team verschiedene Verfahren.
Am vielversprechendsten war es, die Pulver trocken in einer Form aufeinanderzuschichten. Dabei brachte das Team neben Kathoden-, Anoden- und Elektrolytschicht Zwischenschichten ein, um den Elektrolytanteil nicht allzu abrupt ansteigen zu lassen. Diese graduellen Übergänge verringern mechanische Spannungen und verbessern Übergangswiderstände in der gesinterten Batterie. Die gefüllte Form wurde in eine Sinterpresse eingelegt, genauer gesagt einer FAST/SPS-Sinterung unterzogen. Dabei werden die Materialien unter hohem Druck und vergleichsweise niedrigen Temperaturen mit einem Stempel zusammengedrückt. Statt Stunden, die bei herkömmlichen Sinterverfahren nötig wären, dauert dies nur wenige Minuten. »Über dieses Verfahren lassen sich mehrere gradierte Schichten von Kathode und Separator in einem einzelnen Herstellungsschritt produzieren«, fasst Heldt zusammen, »was den Arbeitsaufwand erheblich reduziert und eine spätere Skalierung zu größeren Durchsätzen erlaubt.« Die Basis für eine industrielle Produktion der Festkörperbatterien sei damit also gelegt.
Quelle: Fraunhofer IPA | www.solarserver.de © Solarthemen Media GmbH