Speicher: Von der Bastelbude zur Serienproduktion
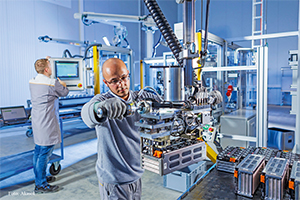
Schon Ende der 80er und in den 90er Jahren gab es mit der Akademischen Solartechnikgruppe der TU Darmstadt Akasol e.V. ein engagiertes Team, das Elektrofahrzeuge konstuierte. Es entstanden der „Pinky” der „Chili” und die „Akabine” bzw. der „Oscar” (siehe Solarthemen 21, 71 und 169), zweisitzige Elektrofahrzeuge mit geringen Verbrauchswerten – Bastelarbeiten auf sehr hohem Niveau. Trotz aller Bemühungen gingen sie nie in Serie. Fast von Anfang an dabei war Felix von Borck. 2008 gründete er mit Björn Eberleh und dem Hauptgesellschafter Sven Schulz die Akasol GmbH. Sie wollen Batteriesysteme bauen, vor allem für große Fahrzeuge: Busse, LKW, Züge und Boote. Im November 2017 feiern sie im hessischen Langen die Eröffnung von Europas größter Serienproduktion von Batteriesystemen für Nutzfahrzeuge. Die Produktionskapazität liegt bei 600 MWh – das reicht für rund 3000 Elektrobusse. „Wir sind auf die Massenfertigung vorbereitet“, sagt Schulz, der Vorsitzende der Geschäftsführung der Akasol GmbH. Er blickt auf einen Wachstumsmarkt für Hybrid- und E-Busse, der jährlich um 35 Prozent zulegen könnte. Denn den Tests von Flottenbetreibern folgten nun die Großaufträge. Großserie als Herausforderung Die Herausforderung für ein Unternehmen wie Akasol besteht darin, die richtigen Lithium-Ionen-Zellen einzukaufen und wettbewerbsfähig und sicher in ein Batteriesystem zu integrieren. Akasol fertigt selbst keine Batteriezellen. Dies birgt die Chance, auf dem Weltmarkt bei Überkapazitäten Zellen zu attraktiven Preisen einkaufen zu können – und das Risiko, bei Knappheiten möglicherweise an Zellmangel zu leiden. Akasol verfolgt damit eine ähnliche Strategie wie die Batterie-Tochter der Daimler AG, die Daimler Accumotive GmbH & Co. KG, die gerade im sächsischen Kamenz Richtfest für ihr zweites Werk feierte. Hier sollen Batterien vor allem für Fahrzeuge, aber auch stationäre Speicher gebaut werden. „Heute sind Zellen commodities”, erklärt Elisa Pee, Pressesprecherin der Daimler AG. „Das heißt: Wir können bei demjenigen kaufen, der die geringsten Kosten und die beste Qualität bietet. Alle Autohersteller haben praktisch die gleiche Chemie im Einsatz.” Daimer könne sich nicht über die eingesetzte Zelle differenzieren, sondern über die Effizienz des Batteriesystems. „Anders sieht das in der nächsten Generation der Zelltechnik, der Post-Lithium-Ionen-Technik, aus”, so Pee, „deren Serienreife ab 2025 zu erwarten ist.” Aber auch diese sei aus Sicht von Daimler nicht zwingend ein Geschäft für einen Autohersteller. TerraE will Zellen bauen Derzeit werden Batteriezellen vor allem in Asien produziert. Mit der TerraE Holding GmbH steht aber ein Frankfurter Unternehmen in den Startlöchern. In der nächsten Zeit gehe es um eine erste Fertigung mit einer Zellproduktionskapazität von 1,5 GWh, erklärt Holger Gritzka, CEO der TerraE Holding GmbH, gegenüber den Solarthemen. Damit solle ein „Proof of Concept” erreicht und demonstriert werden. „Wir wollen zeigen, dass es geht.“ Der Aufbau der Kapazität solle parallel zum Absatz erfolgen. Die geplante Erweiterung auf 34 GWh werde auf Grundlage von geschlossenen Lieferverträgen umgesetzt. Dann sei es auch kein Problem, den Kapazitätsaufbau zu finanzieren. Er wisse schon, wo diese Fabrik aufgebaut werden soll, wolle dies aber erst später, zum gegebenen Zeitpunkt, bekannt geben. Chancen für TerraE sieht Gritzka in den Produktionstechnologien, die wesentlich kostengünstiger als bei einigen Mitbewerbern seien. Zudem biete ihre Technologie mehr Performance – was in der Serienproduktion noch zu beweisen ist. Dabei sei generell wichtig, das Know-how von Partnern in den Aufbau der Produktion zu integrieren. Das betreffe den Maschinenbau, aber auch andere Bereiche und auch die Kooperation mit schon bestehenden Zellherstellern. „Ohne Technologiepartner wird es nicht funktionieren.“ Gritzka erwartet eine dynamische Marktentwicklung. Für TerraE erklärt er: „Wir sind in einer permanenten Aufwärtsbewegung.“ Der Markt für Batteriezellen werde schneller wachsen als das Angebot. In der Folge erwartet er den Aufbau einer Reihe von Zell- und Batteriefabriken weltweit und an unterschiedlichen Standorten in Europa. Perspektivisch werde es keinen Sinn machen, Lithium-Ionen-Zellen zu importieren. Aufgrund der Transportkosten, aber auch wegen der vorhandenen Einfuhrzölle würden die Zellen künftig eher dort produziert, wo sie gebraucht werden. Dies werde erst recht bei Batteriemodulen und -packs der Fall sein. Als Player sieht Gritzka die jetzt schon bekannten. Es seien keine weiteren großen Gründungen abzusehen. Beim weiteren Ausbau der Kapazitäten werde sich der Markt weiter differenzieren. „Für die unterschiedlichen mobilen und stationären Anwendungsbereiche wird es dann jeweils Fabriken geben, die die dafür am besten geeigneten Zellen herstellen.“ Konkurrenz aus Asien Konkurrenz in Europa hat Gritzka auch von Herstellern aus Asien zu erwarten. So kündigte das japanische Unternehmen GS Yuasa Ende Januar an, im ungarischen Miskolc eine Fabrik mit einer Produktionskapazität von 500000 Batterien zu bauen. Die Zellen sollen zunächst aus Japan bezogen werden. GS Yuasa kann sich künftig aber auch die Produktion von Zellen in Europa vorstellen. Im Batteriesektor werden jetzt Geschichten geschrieben – so wie die von den drei Kreisel-Brüdern aus dem österreichischen Freistadt, die 2012 in ihrer Werkstatt ein erstes Fahrzeug zum Elektroauto umbauten und dann mit Know-how und guten Ideen leistungsfähige Speicher entwickelten. Im Herbst vergangenen Jahres eröffneten sie ihre eigene Fabrik zur Batterieproduktion, in der sie Ende dieses Jahres schon 200 Mitarbeiter beschäftigen wollen. EU-Kommissionsvizepräsident Maroš � efčovič will solche Entwicklungen ebenfalls vorantreiben. Am 22. und 23. Februar will er den Fahrplan für eine EU-Batterieallianz vorstellen. Text: Andreas Witt Foto: Akasol