Neue Wafer-Formate: Herausforderung für Maschinenbauer
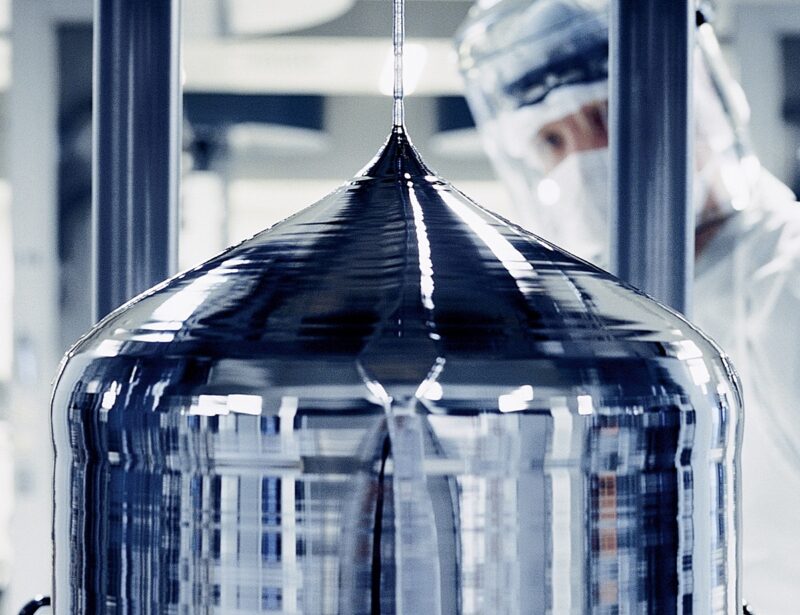
Markus Fischer, Vizepräsident für Forschung und Entwicklung bei der Hanwha Q-Cells Deutschland, hat ein Update der Internationalen Technologie Roadmap für Photovoltaik (ITRPV) im Rahmen des 10. Solar World Kongress in Shanghai vorgestellt. Neben dem Technologiereifegrad, der für ausgewählte Parameter der Kristallisation, Waferherstellung, Zellfertigung und Modultechnologie implementiert wurde, beschäftigt sich das Update mit dem aktuellen Thema der ständig wachsenden Wafer Größe.
Die ITRPV betrachtet bereits jährlich die Entwicklung verschiedener Wafer-Größen und zeigte in der im März veröffentlichten Ausgabe, dass dieser Bereich von einer Vielzahl an neuen Formaten geprägt ist. Für deutsche Maschinenbauer ist eine Standardisierung der Wafer-Größe von großem Interesse. Aber wie genau steht es um die Implementierung alternativer Wafer-Größen in bestehenden Produktionslinien? Eben diese Frage sollte im Rahmen des Updates der ITRPV beantwortet werden.
Die Ergebnisse zeigen, dass lediglich die Wafer-Größen kleiner M4 ohne große Modifikationen in bestehenden Linien implementiert werden können. Ab der Wafer Größe M4 ist eine Implementierung nur mit Upgrades von existierenden Linien möglich, während zur Installation von Wafern mit Größen ab M6 neue Linien benötigt werden. Dieser Trend ist konsistent bei der Betrachtung der Herstellung von mono- und multikristallinen Silizium-Wafern und auch bei der Zell- und Modulfertigung.
Kapazitätsdifferenz bei Front- und Back-End-Prozessen
Die jährliche Abfrage des Technologiereifegrades für verschiedene, ausgewählte Parameter in der Herstellung von kristallinen Silizium-Solarzellen zeigt an, ob Verbesserungsmaßnahmen schneller in die Massenproduktion implementiert werden können oder ob vor einer Einführung bestimmter Technologien in die Massenproduktion weitere F&E-Arbeiten erforderlich sind. Um zwischen vier Reifegraden zu unterscheiden, wird eine Farbmarkierung verwendet.
Ein wesentlicher Faktor zur Kostenreduktion und somit auch zur Wettbewerbsfähigkeit stellt der Durchsatz verschiedener Anlagen dar. Bei der Betrachtung von chemischen und thermischen Prozessen sowie Metallisierungs- und Klassifizierungsprozessen zeigt sich eine große kapazitative Differenz des potenziell möglichen Durchsatzes. Der Durchsatz von ca. 9000 Wafern pro Stunde bei den Front-End-Prozessen (chemisch und thermisch) wird voraussichtlich im Jahr 2021 ohne große Anpassungen in der Massenproduktion implementiert. Hingegen wird im Rahmen der Back-End-Prozesse deutlich, dass bereits die Durchsatzkapazität von 6000 Wafern pro Stunde weitere Entwicklungsarbeit benötigt.
Ein Update der 10. Edition der ITRPV steht hier zum Download zur Verfügung.
5.11.2019 | Quelle: VDMA | solarserver.de © EEM Energy & Environment Media GmbH