Recycling ohne Schreddern: KIT will Batterie-Rohstoffe effizienter wiedergewinnen
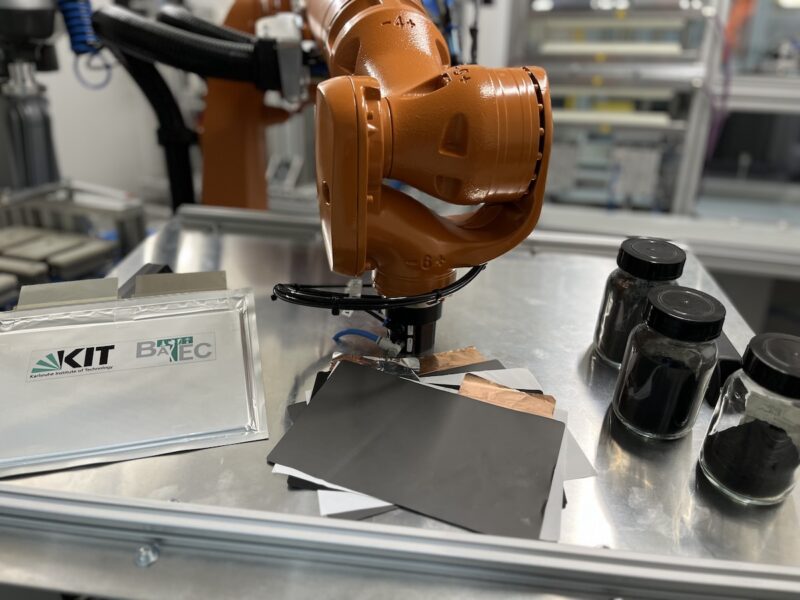
Um knappe Rohstoffe für die Energiewende effizient zu nutzen, arbeiten viele Forschungsinstitute und Firmen an Recycling-Verfahren für Batterien. Aktuelle Recycling-Verfahren zerkleinern dafür die Batterie-Zellen und lösen die Aktivmaterialien bis auf die Molekülebene auf, um diese später in Form von Metallsalzen aus der Flüssigkeit zu gewinnen, erklärt das KIT. So könnten bis zu 90 Prozent der kritischen Elemente – etwa Kobalt, Nickel und Mangan – wiedergewonnen werden. Allerdings brauche man für diese Rückgewinnung viel Energie und Chemikalien. Im Anschluss müsse man noch mehr Energie und Rohstoffe investieren, um daraus wieder neue Batterien zu machen. Forschende am KIT wollen den Weg abkürzen und die Aktivmaterialien aus alten Batterien und Produktionsausschüssen direkt recyceln.
„Dabei werden die Aktivmaterialien nicht mehr vollständig aufgelöst. Stattdessen werden sie in die einzelnen Zellbestandteile zerlegt und dann mechanisch getrennt, um sie möglichst rein zurückzugewinnen“, erklärt Marco Gleiß vom Institut für Mechanische Verfahrenstechnik und Mechanik. Er koordiniert das Verbundprojekt „Agile Prozesskette zum direkten Recycling von Lithium-Ionen-Batterien und Regeneration der Aktivmaterialien“ (DiRecReg) auf Seiten des KIT.
Einen ähnlichen Ansatz stellte das KIT bereits im Frühjahr vor. Dabei erklärten die Forschenden, auf diesem Wege auch das besonders knappe Lithium zurückgewinnen zu können.
Flexible Prozesskette für das Recycling entwickeln
Bisher gebe es in der Industrie allerdings keine Prozesskette für das direkte Batterie-Recycling. Es fehlt bereits an wirtschaftlichen Wegen, um die unterschiedlichen Batteriepacks zu zerlegen. Und hat man Rezyklate gewonnen, kann man bisher nicht klar beurteilen, wie gut diese noch nutzbar sind und wie sie sich in einer neuen Batterie verhalten werden. „Diese kritischen Punkte greift unser Verbundvorhaben auf“, sagt so Projektkoordinator Dr. Thomas Dreyer von der Weber Ultrasonics AG.
Ziel ist es, eine agile Prozesskette für das Recyceln von Lithium-Ionen-Batterien zu entwickeln. Außerdem sollen die wiedergewonnenen Aktivmaterialien regeneriert werden. Der Prozess soll dabei so variabel sein, dass sich auf verschiedene Ausgangsmaterialien der Batterieproduktion und für Produktionsausschüsse zuschneiden lässt und unterschiedliche Batterieformate und Bauarten verarbeiten kann. „Ziel ist es zudem, die energieintensiven Prozessschritte der zurzeit eingesetzten Recycling-Verfahren zu ersetzen und nachhaltig recycelte, hochwertige Sekundärmaterialien im Sinne einer Kreislaufwirtschaft zu liefern“, so Gleiß.
Das Projekt DiRecReg hat eine Laufzeit von drei Jahren und wird vom Bundesforschungsministerium mit 2,95 Millionen Euro gefördert. Das Projektkonsortium steht unter der Federführung der Weber Ultrasonics. Es besteht aus zehn Partnern – darunter vier Institute des KIT – sowie einem assoziierten Partner.
28.11.2023 | Quelle: KIT | solarserver.de © Solarthemen Media GmbH