Gesa Beck im Interview zum Recycling von Photovoltaikmodulen
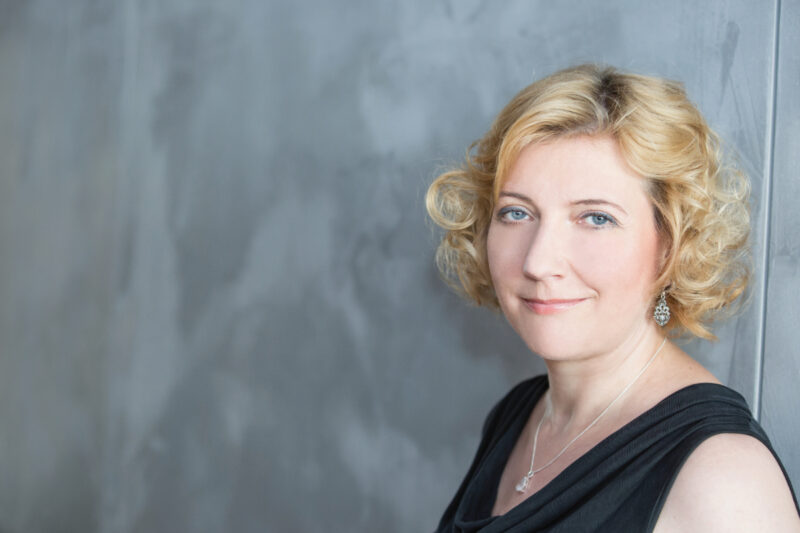
Solarthemen: Die Solarbranche befasst sich schon einige Jahre mit dem Recycling von Photovoltaikmodulen. Wie würden Sie den jetzigen Stand einschätzen?
Gesa Beck: Zunächst ist zu sagen, dass noch gar nicht so viele Abfälle vorhanden sind, als dass das Recycling von Photovoltaikmodulen besonders wirtschaftlich wäre. Es gibt einige interessante Entwicklungen im Bereich der Forschung auch auf europäischer Ebene, darunter unser Projekt mit unserem Ansatz. Zurzeit sehen wir im Markt sonst eher ein Downcycling mit sehr einfachen Methoden. So wird das Glas von den Modulen gelöst, zerkleinert und als relativ unreine Fraktion zu einem Füllmaterial verarbeitet. Die Aluminiumrahmen und die Kabel werden ebenfalls abgetrennt und einer Verwertung zugeführt – die haben auch einen gewissen Wertanteil. Doch bei allem, was technologisch etwas aufwendiger ist, gibt es noch keine im gewerblichen Sektor angewendeten Verfahren. Das spielt sich nur im Bereich Forschung und Entwicklung ab. Denn für diese weiterführenden Verfahren kommen jährlich einfach noch zu wenig End-of-Life-Module zusammen.
Sie hatten es angesprochen, doch was könnten wir konkret schon recyceln und dem Kreislauf wieder zuführen?
Glas ist ein wesentlicher Bestandteil beim Recycling von Photovoltaikmodulen
Das Glas macht die größte Masse an einem Solarmodul aus. Beim Glas gibt es verschiedene Qualitätsstufen. Das Solarglas ist als eisenarmes Flachglas mit einer bestimmten Oberflächenstruktur relativ hochwertig. In Freiberg gibt es Ansätze, das Glas als Ganzes weiternutzen zu können. Auch in unserem von der Deutschen Bundesstiftung Umwelt unterstützen Projekt haben wir die Verfahren so entwickelt, dass wir ganze Scheiben aus dem Modul herauslösen. Allerdings wird dies wohl nicht großtechnisch realisiert werden.
Wir haben eine Marktanalyse erstellt und nach potenziellen Kunden gesucht. Die sind kaum vorhanden. Es wird eher eine Nische sein, dass die kompletten Scheiben für neue Produkte nutzbar sind. Insofern ergibt es mehr Sinn, die Gläser zu zerkleinern, aber in einem möglichst reinen Zustand in die Flachglasproduktion einzuspeisen. Es wäre die nächste Stufe, daraus wieder neue Fensterscheiben herzustellen. Andere nicht so reine Fraktionen könnten in die Flaschenproduktion wandern. Wir haben dann die Kunststoffe, die Rückseitenfolien und die Laminierfolien. Die Rückseitenfolien werden nach meinem Kenntnisstand im gewerblichen Bereich noch nicht zurückgewonnen. Es wäre aber möglich. So zeigt es auch das von uns entwickelte Verfahren. Es wird mehr und mehr PET eingesetzt. Und PET als Thermoplast lässt sich in andere Produkte umformen. Die Laminierfolie, das EVA, wird in der Regel nicht wiederverwendet. Hier kann man bei den meisten Verfahren nur sehen, wie man sie sozusagen los wird.
Was kann man da machen?
Man kann das EVA auflösen oder thermochemisch umsetzen. Letzteres haben wir auch in unserem Projekt realisiert. Wir nutzen eine Mikrowellenpyrolyse, das ist eine relativ energiearme Pyrolyseform. Das Ergebnis ist ein Pyrolyseöl, das über die chemische Industrie wieder zu einem Rohstoff für neue Kunststoffe wird.
Solarzellen von besonderen Interesse
Was ist mit den Solarzellen?
Das sind die eigentlich interessanten Materialien, würde ich sagen. Wir haben das Silizium der Zellen und deren Kontakte aus Kupfer und Silber, wobei die neueren Module immer weniger Silber enthalten. Silber ist natürlich das wertvollste Material, aber davon kommt nicht viel zusammen. Zuerst lag das bei 0,01 Prozent, aber das wird immer weniger. Außerdem haben wir teils noch Aluminiumbänder. Und mit unserem Prozess sind wir die Einzigen auf dem Markt, soweit ich das übersehe, die in einem Einschrittprozess die Metalle ablösen und sukzessive einzeln hochrein zurückgewinnen können. Unsere Expertise ist die Elektrochemie ohne irgendwelche Zwischenschritte. Wir brauchen dafür sehr wenig Energie. Das sind nur ein, zwei Volt bei Raumtemperatur. Unser Elektrolyt ist bioabbaubar und den können wir auch zirkulieren lassen. Ich glaube, dass wir gut behaupten können, ein sehr gutes Green-Chemistry-Verfahren zu haben. Das Ergebnis sind sehr reine Materialien, mit denen man neue Produkte herstellen kann.
Gibt es dafür schon eine kommerzielle Nutzung?
Wir haben dafür einen Partner, eine englische Firma, die mit unseren Materialien im Printverfahren flexible Photovoltaikmodule produziert. Das Unternehmen ist auf Biopolymere spezialisiert. Sie drucken mit unseren Metallen und dem recycelten Silizium neue Photovoltaikmodule. Das Einzige, das wir mit unseren Verfahren nicht abtrennen können, sind die Dotierungen. Bei unserer Partnerfirma ist es hier der Ansatz, dass sie dies sozusagen mitteln, kristallin machen und zudotieren. Das wollen wir in einem gerade beantragten Forschungsprozess weiter aufbauen.
Nun hängt das Recycling auch davon ab, wie teuer bestimmte Stoffe sind. Wir hatten eine Zeit, da war Silizium sehr knapp und unglaublich wertvoll. Da wurden die ersten Verfahren entwickelt, um Silizium aus Solarzellen wiederzugewinnen. Ist das noch sinnvoll?
Silizium derzeit nicht so relevant
Wir gehen an das Verfahren nicht thermisch heran. Um das hochreine Silizium wiederzugewinnen, müssten wir ein Schmelzverfahren einführen. Wir sehen darin derzeit aber keinen Wert. Der preisliche Unterschied zwischen dem reinen und dem ganz hochreinen Silizium ist zurzeit nicht besonders hoch Generell sind die Materialien, die in die Photovoltaik gehen, heute nicht so besonders teuer. Das teuerste, das immer weniger für Solarmodule verwendet wird, ist das Silber. Wir analysieren unsere Prozesse mit einer Materialflusskostenrechnung immer sehr detailliert, um deren Wirtschaftlichkeit beurteilen zu können. Ein Ergebnis ist, dass wir uns selber tragen können, wenn wir 20 Module zu den jetzigen Kosten aufbereiten können, wobei die Infrastruktur dabei nicht berücksichtigt ist. Das heißt, allein die Kosten für Materialien und die Mitarbeiter sind abgedeckt. Um auch eine eher industrielle Infrastruktur refinanzieren zu können, wären 500 Module am Tag erforderlich.
20 Module sind aber sehr wenig, wohl Handarbeit. 500 Module klingt auch noch nicht nach so viel. Wie sieht das aus, wenn man die Verfahren in einen mehr industriellen Prozess überführt?
Bei den 500 denken wir schon an einen industriellen Prozess. Die Konzepte dafür stehen auch. Die Module würden wir über Transportbänder in die verschiedenen Geräte einführen. Unser Prozess ist aber nicht nur auf die Photovoltaikmodule fokussiert. Wir haben zwei Schritte, die abgesehen von der Pyrolyse wesentlich sind, also die chemische Delamination und die Elektrochemie. Und diese beiden Schritte können wir auch für andere Abfallfraktionen nutzen. Das heißt, wir können auch flexibel mit anderen Abfällen arbeiten – und flexibel muss man als Recycler auch sein, um wirtschaftlich arbeiten zu können, weil die Preise sehr volatil sind.
Nun gibt es mehr und mehr Unternehmen, die Glas-Glas-Module herstellen. Macht das beim Recycling einen Unterschied?
Wir haben parallel, aber das ist im Labormaßstab und noch nicht ausgereift, noch einen anderen Ansatz. Wir haben ja für die komplett herausgelösten Scheiben keine Abnehmer gefunden. Daher beginnen wir nun mit dem Schreddern des Glases. Und das können wir auch mit den Glas-Glas-Modulen machen, weil wir auch die Delaminierung gut in den Griff bekommen.
Nachfrage nach den gewonnenen Rohstoffen beim Recycling von Photovoltaikmodulen
Wo gibt es denn eine Nachfrage nach den gewonnenen Rohstoffen?
Im Rahmen unsere Projekts haben wir eine Marktrecherche gemacht und am Ende einen Flachglashersteller gefunden. Für das Kupfer ist es kein Problem, Käufer:innen zu finden. Für das Silizium haben wir nur unseren Partner in England.
Das ist nun in einem geringen Maßstab und es ist deutlich mehr an alten PV-Modulen zu erwarten? Bauen wir dann beim Recycling sehr große Halden an Rohstoffen auf?
Es gibt ja nun den Ansatz, dass die Module, die aus den Parks oder anderen Anlagen zurückkommen, gut und vorsichtig gesammelt werden, um möglichst keine Defekte zu verursachen. Der erste Schritt ist dann zu prüfen, ob sie grundsätzlich noch funktionsfähig sind. Die können – möglicherweise nach einer einfachen Reparatur – noch ein zweiten Leben bekommen, zum Beispiel in afrikanischen Ländern. Teils wird das als Abfallverschiffung kritisiert, aber wir sind hier involviert. Ein Kollege von mir, der in diesen Ländern ausbildet, kann berichten, dass die Menschen dort von diesen Anlagen profitieren. Unsere Abschätzung zu den 500 Modulen beruht aber auch auf einer Marktanalyse, dass einige Module gar nicht zum Recycling, sondern direkt in ein Second-Life kommen, und andere von den anderen rund 20 Recycling-Unternehmen verarbeitet werden.
Aber wenn nun Module vor allem aus China kommen, wie nutzen wir dann das gewonnene Silizium?
Das Silizium ist natürlich das Sorgenkind. Aber man kann das in unterschiedlichen Qualitäten in Deutschland nutzen, zum Beispiel als Ferrosilizium in der chemischen Industrie. Als Reduktionsmittel wäre es die letzte Stufe. Verkauft bekommt man es, die Frage ist nur zu welchem Preis.
Interview: Andreas Witt | www.solarserver.de © Solarthemen Media GmbH