Fraunhofer: Serienfertigung für Bipolarplatten von Brennstoffzellen
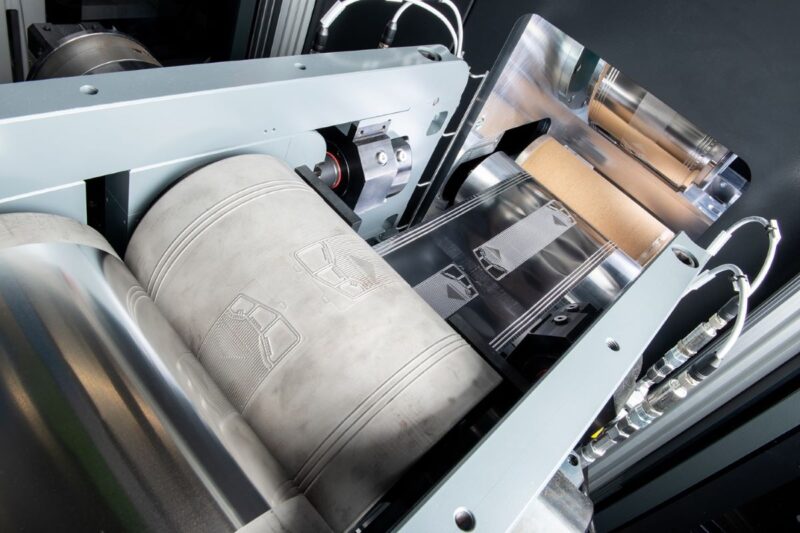
Forschende an Fraunhofer-Instituten wie dem für Produktionstechnologie IPT arbeiten an einer kostengünstigeren Serienfertigung von Bipolarplatten. Das ist das Herzstück einer Brennstoffzelle. Wie das Fraunhofer IPT mitteilte, sind ausgereifte Produktionstechnologien für die Serienfertigung eine Voraussetzung, um einen flächendeckenden Einsatz der Brennstoffzelle zu erreichen.
Die Entwicklung industrieller Technologien für die Produktion der Brennstoffzelle steht im Zentrum des Forschungsprojekts »H2GO«. Dort arbeiteten 19 Fraunhofer-Institute zusammen an verschiedenen fertigungstechnischen Herausforderungen. Dazu zählen effiziente Prozesse und Produktionssysteme sowie der dazugehörige Maschinen- und Anlagenbau.
Die Herstellung von Bipolarplattenhälften in der Großserie sei eine Herausforderung für die blechverarbeitende Industrie. Im Forschungsprojekt entwickeln die Forschenden des Fraunhofer IPT zwei verschiedene Prozesse zur Formgebung für Bipolarhalbschalen. Das sei zum einen die diskrete Umformung, bei der Werkzeuge ein Brennstoffzellen-Design auf ein metallisches Blech prägen. Zum anderen gehe es um die Rolle-zu-Rolle-Umformung. Dabei bringe eine Prägewalze das Design der Brennstoffzelle auf eine metallische Folie auf.
Umformverfahren bisher nicht serientauglich
Während die hochwertige Einzelfertigung von Bipolarplattenhälften im Labormaßstab gelinge, habe sich bisher kein diskretes, serientaugliches Umformverfahren am Markt etablieren können, mit dem sich eine schnelle Taktung oberhalb von 60 Hüben pro Minute bei gleichbleibend hoher Umformqualität erzielen lasse. Um das zu ändern, untersuchen die Wissenschaftlerinnen und Wissenschaftler des Fraunhofer IPT die Umform- und Stanzwerkzeuge sowie die zugehörigen Pressensysteme und die darin ablaufenden Prozesse.
Das Projektteam verkette dafür die erforderlichen Bearbeitungsschritte in einem Folgeverbundwerkzeug. Zusätzlich zu den bereits vorhandenen Stanz- und Umformeinheiten integriere das Forschungsteam ein Erwärmungsmodul, das das dünne Blechmaterial leichter umformbar macht.
Analyse von Einzelprozessen
Sowohl bei der diskreten Fertigung im Folgeverbundwerkzeug als auch bei der kontinuierlichen Fertigung im Rolle-zu-Rolle-Verfahren durchlaufe eine Bipolarplattenhälfte eine Vielzahl von Einzelprozessen. Neben der eigentlichen Formgebung existierten weitere vor- und nachgelagerte Prozessschritte wie die Reinigung, der Dichtungsauftrag oder die Laserbearbeitung der Komponente. Um den Weg der Bipolarplattenhälfte durch die Prozesskette nachvollziehen zu können, setzten die Forschenden auf zusätzliche Beschriftungs- und Scannermodule. Damit erhalte jedes Werkstück im ersten Prozessschritt einen Data-Matrix-Code (DMC), der in Folgeprozessen ausgelesen und erfasst wird.
Mit dem DMC können die Forschenden Qualitäts- und Maschinendaten lückenlos zurückverfolgen und auswerten. Wertvolle Informationen lassen sich so ableiten, anhand derer die Wissenschaftlerinnen und Wissenschaftler die Fertigung gezielt optimieren und so die Produktionseffizienz steigern können. Zudem können sie Muster und Trends identifizieren, die zur Verbesserung der Produktqualität und zur Beseitigung von Fehlerquellen beitragen, damit sich Ausschuss und Kosten noch weiter reduzieren.
Das Forschungsprojekt »H2GO« erhält im Rahmen des Nationalen Innovationprogramms Wasserstoff- und Brennstoffzellentechnologie Phase 2 (NIP II) eine Förderung des Bundesministeriums für Digitales und Verkehr.
Quelle: Fraunhofer IPT | www.solarserver.de © Solarthemen Media GmbH